Three innovations that will soon be daily fare in forest industry
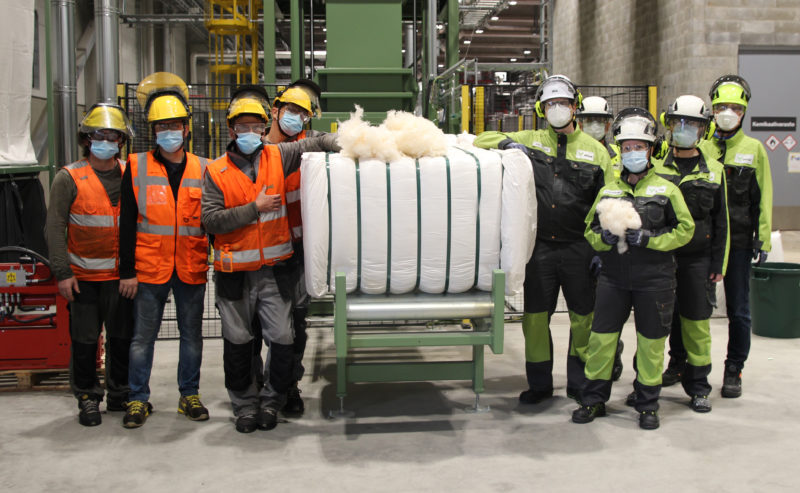
Research carried on by the forest industry leads to new innovations and commercial production. Solutions now tested include textile material made from pulp and self-driving lorries. A pulp-based printing material for 3D printing is already in commercial use.
Metsä Spring, the innovation company of the Metsä Group, passed an important milestone in September 2020: its pilot plant in Äänekoski, Central Finland, produced the first batch of a new type of textile fibre manufactured from wood pulp.
The project was started in 2012, and the decision to invest in a pilot plant was taken in 2018. The commissioning of the pilot plant, involving several representatives of equipment suppliers, started in late February 2020.
‘However, due to the Covid-19 pandemic, the testing phase was delayed so that the last tests could be introduced only in August,’ says Niklas von Weymarn, CEO of Metsä Spring. The main objective of the tests is to verify that the manufacturing devices function as was previously planned.
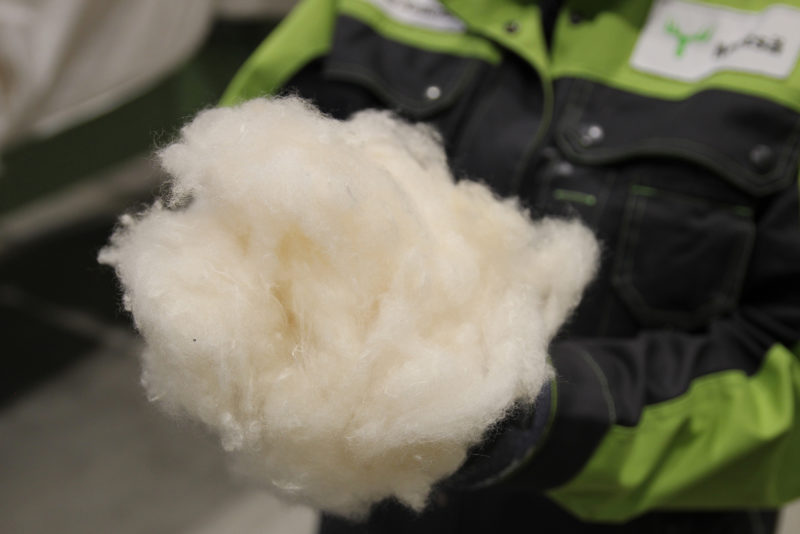
Along the tests, the first batch of the product, a staple fibre suitable for producing textiles, was available in September.
‘The batch was a few hundred kilos in weight. That in itself wouldn’t make very much textile fibre, and since it was the very first batch, its quality can also be further improved,’ says von Weymarn.
‘Getting the production up and running is an important milestone in the pilot plant project. It’s an ideal example of collaboration between a number of actors,’ he continues.
Test runs of the equipment are continuing and will be completed before winter, after which the aim will be to prove that the new manufacturing method works on an industrial scale.
Provided that the results are favourable, Finland may see a mill that produces textile fibre on a considerably larger scale.
To operate the pilot plant, Metsä Spring has established a joint venture named MI Demo with the Japanese Itochu Corporation.
Automated lorry transports wood chips at Stora Enso mill
Stora Enso began to test a remotely-steered lorry at its Uimaharju Mill in Joensuu, eastern Finland, in March 2020. The tests aim at determining how far automated transport of this type can cut down costs and emissions and improve safety.
In future, automated transport may be of considerable significance for the forest sector in Finland. Logistics is a survival issue for the sector: distances are long, felling sites are small and far from each other, and the markets for forest products are situated a long way from the production plants.
Even now, the routes of timber lorries between forest sites and production plants are optimized by computer. In future the cost and environmental impact of transport will be further reduced by using better fuels, for example. Another, if distant, objective is to use automated lorries for at least some of the routes.
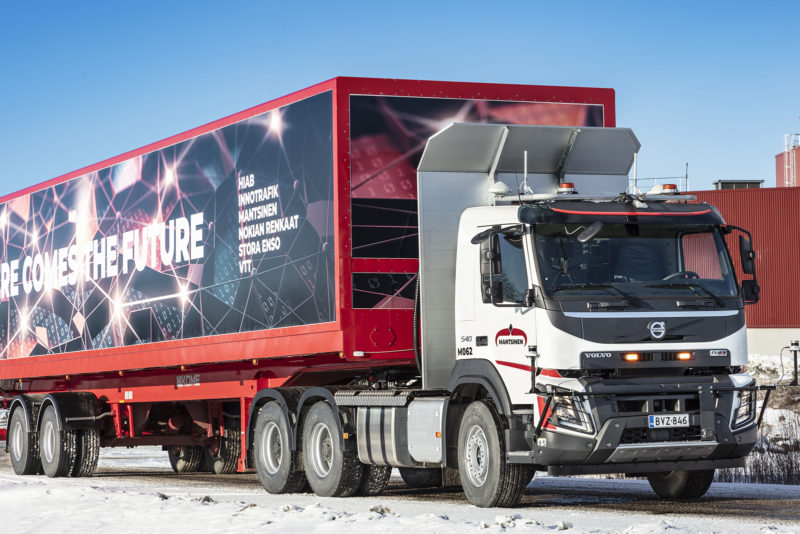
In Stora Enso’s experiment, the lorry transports wood chips from a sawmill for raw material to a pulp mill on the same site. The vehicle travels the 1.4-kilometre distance about 15 times a day, at a maximum speed of 20 kilometres per hour.
Traffic safety along the route is already better, thanks to new safety equipment such as smart traffic lights. Emissions are also expected to decrease, with automation optimizing the engine operation and the choice of route. This will also reduce costs.
‘The lorry is continuously learning how to travel along the route and to pay attention to other traffic. For now, the driver sits in the lorry to ensure a smooth transit and safety,’ says Lauri Kuusisto, Director of Operations at Stora Enso, Wood Supply Finland.
The driver takes a more active role at crossroads, for example. ‘Fairly soon we’ll be able to test fully automated operation. The plan for next year is that the driver will steer the lorry by remote control,’ says Kuusisto.
‘We’ll be able to assess the results after using the lorry a bit longer. By now it’s safe to say that everyone concerned is eagerly looking forward to the results,’ says Kuusisto.
The testing is scheduled to continue until the autumn of 2021 at least. The project partners include Mantsinen Group, the company operating the wood chip transport; Hiab, which has supplied the control system and equipment for the lorry; and VTT Technical Research Centre of Finland, involved in the development.
The safety aspects have also involved the InnoTrafik company and VTT. In addition, Nokian Tyres tests smart tyres equipped with Intuitu sensors in the project. ‘This extensive collaboration reflects our philosophy that innovations do not come about in isolation, but in collaboration,’ says Kuusisto.
3D production takes manufacturing close to the consumer
This year, the Formi product family by UPM Biocomposites has been augmented with the new UPM Formi EcoAce material. The products are developed for injection moulding, with the exception of UPM Formi 3D, which is envisaged for large-scale 3D printing. In injection moulding, a molten and fluid material is packed under pressure into a mould, where it solidifies and takes on the shape of the mould.
In general, the products in the UPM Formi family are made of cellulose fibres or mechanically ground wood fibre and a biobased polypropylene or polylactide (PLA). The renewable-based plastic in EcoAce, however, is made of bionaphtha produced from tall oil, a residual of pulp manufacturing, at UPM’s biorefinery in Lappeenranta, eastern Finland. This means that raw-material of the bioplastic is almost wholly forest-based.
The share of wood-based fibres in materials for injection moulding is 40–60%. The 3D printing material only uses cellulose fibre, whose share is 20%.
The purpose of the fibre in these products is to strengthen the end product, causing it to keep its shape and size during its life cycle. Curved and other challenging shapes can be printed without difficulty.
‘Moreover, using biocomposite gives better quality and precision than previously. The material also gives the end product a wood-like feel, which is much more attractive to consumers than can be achieved with plastic,’ says Eve Saarikoski, Application Manager at UPM.
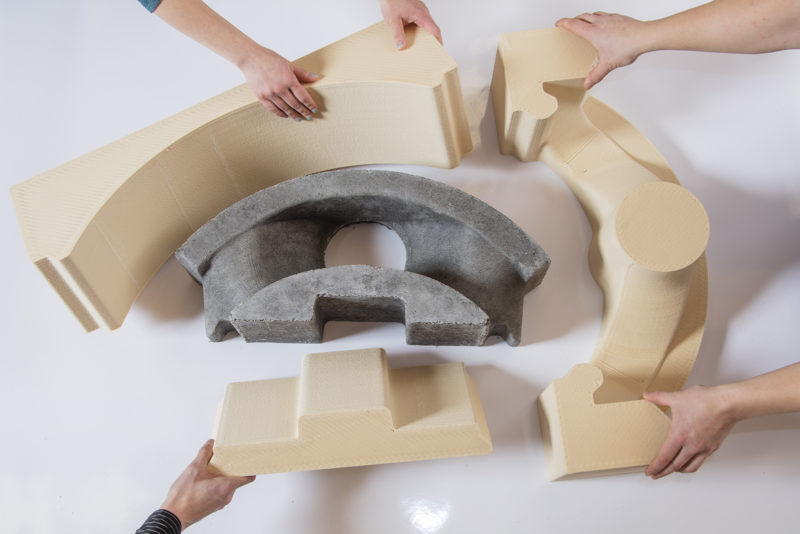
The materials are delivered to the customer as granulates.
Large-scale printing refers to the printing of items with sizes ranging from one metre to 4–5 metres. These include furniture and casting moulds.
3D-printed casting moulds can be used instead of plywood, for example. Plywood can be difficult to bend into shape, unlike 3D moulds made from UPM’s material, which can be shaped in the same way as wood after printing.
What is more, UPM’s material in the casting moulds may be re-used. After, say, a concrete casting mould is no longer needed, it may be crushed and used to make new 3D moulds. Thus the wooden moulds used in casting concrete may become a thing of the past.
‘Manufacturers using the printing method may opt for a model where the customer uses a global catalogue to order a chair, for example, that will then be printed locally. The only thing to transport would be the granulates,’ says Saarikoski. An operation model like this is also possible because the unit cost of printing is more or less the same regardless of how many units are made.
As regards printer capacity and need for printing material, Saarikoski says that one machine could print 1,000–1,500 chairs a year and one chair would take about ten kilos of material. According to Saarikoski, the production volumes of the material are doubling each year.
Wood-based fibres compete for market shares with carbon fibres and glass fibre. The UPM granulates are manufactured at the UPM Biocomposites plant in Lahti, southern Finland.
The company launched the first UPM Formi products in 2011. The 3D product family came to market in 2018.