AI shows forestry operators best routes in forest – warns about ground too soft for harvesters
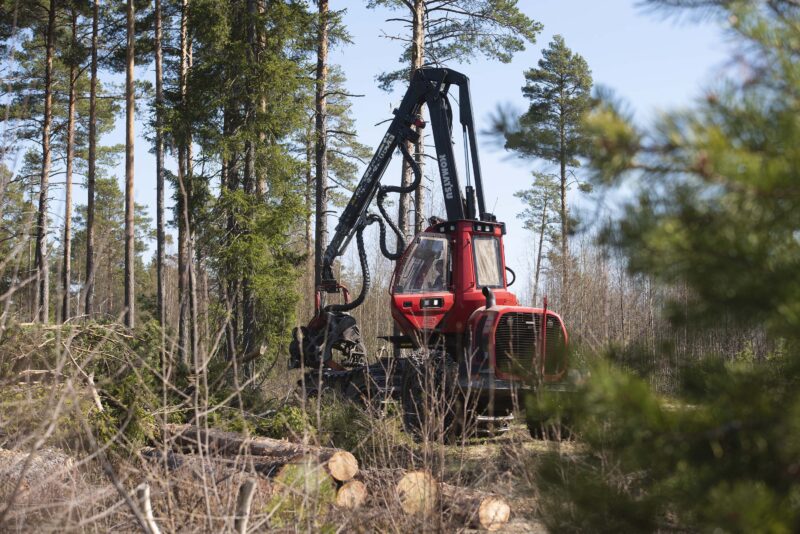
Researchers are developing machine learning methods to help mechanical harvesters to travel more lightly, use less fuel and leave less noticeable strip roads in the forest.
Researchers at the University of Helsinki are developing machine learning methods enabling the harvester to assist the operator in choosing routes that are optimal for both harvesting and nature. The machine could then predict the relevant terrain characteristics even before the actual operation.
’This information will help to optimize the route and assist the operator by telling, for example, where the ground is too soft,’ says Professor Jukka Heikkonen, in charge of the project funded by the Research Council of Finland.
Harvesting operations must be planned so as not to leave too invasive strip roads. The softer the ground, the more difficult it is for the harvester to travel and the more likely it will cause ground damage.
’Harvesting operations must be planned so as not to leave too invasive strip roads. The softer the ground, the more difficult it is for the harvester to travel and the more likely it will cause ground damage,’ Heikkonen notes.
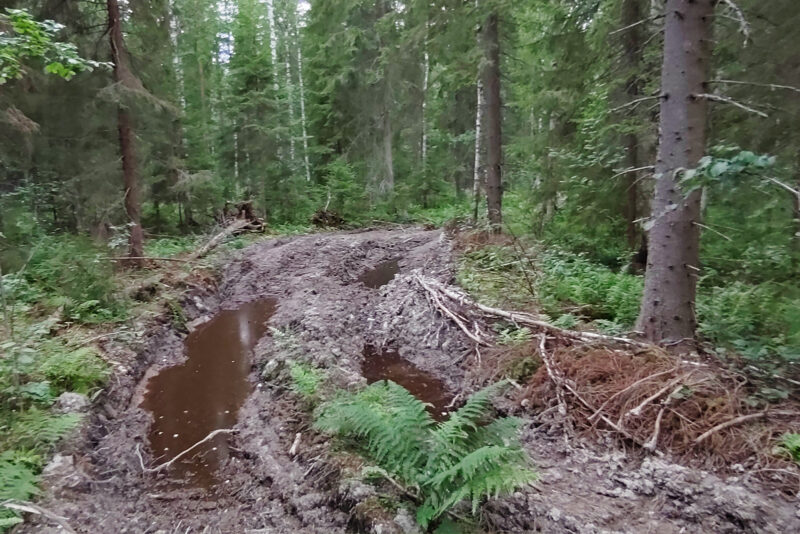
Strip roads, or the tracks left by the harvester, are detrimental to forest growth, increase the risk of diseases and are an eyesore. Travelling across soft ground also increases the rolling resistance and therefore, the fuel consumption and cost.
’The softer the ground, the more probably it will be damaged. The physical quantity used in the study is the rolling resistance factor of the harvester, which describes the ease of travel on a particular stretch of ground,’ Heikkonen says.
According to the Finnish Forest Act, only one fifth of the length of a strip road created to reach a harvesting site may be over ten centimetres in depth. For peatlands, the corresponding depth is twenty centimetres.
Believe it or not – ten amazing facts about mechanized timber harvesting
Map shows ease of travel
Using the figure for ease of travel and the harvester’s rolling resistance, it is possible to create a map showing the conditions most suitable for the strip roads. The map may be used to position the route of forwarders and to schedule the operation.
Measurements of damage caused by strip roads may be combined with open-source forest data and harvester data. This will allow predictions of future damage from the strip roads in a harvesting operation.
The predictions and modelling make use of machine learning, which is capable of combining open-source masses of data, measurement data from harvester sensors and physical models of the terrain.
Combining measurements of strip road damage with open-source forest data and harvester data makes it possible to predict the degree of damage even before the operation.
Moist ground increases resistance
Research results show that the rolling resistance of the harvester is greatest in depressions and on loamy soils. Moist soils increase the resistance. Moistness, in turn, is affected by weather conditions, as well as rain, evaporation and the presence of meltwater.
Data for the research was collected from actual forestry operations in southern Finland. Identifiers linked to geospatial data describing moistness and soil type indicate the ease of travel on a particular site.
Using the soil moistness and the harvester’s rolling resistance data, it is possible to create a forest hydrology model for anywhere in Finland. The terrain data gathered by the harvester is generalized to cover other, corresponding terrains.
’Using the soil moistness and the harvester’s rolling resistance data, it is possible to create a forest hydrology model for anywhere in Finland. The terrain data gathered by the harvester is generalized to cover other, corresponding terrains. This also makes use of forest resources data, among other things,’ says Heikkonen.
The aim is to plan harvesting operations with the knowledge of ’where to go and when’. Knowing this would not only help the people planning the harvesting, but also the practical work of the harvester operator. The objective is to achieve an automatic route planning, which will serve as a basis for autonomous harvesters.
Factors affecting the ease of travel include the load-bearing capacity of the soil, the steepness of slopes and areas where the harvester may not enter. Other important factors include type of terrain, vegetation, climate, weather, ground-level moistness and the machinery used in harvesting.
Heikkonen points out that once an operation has been scheduled, it must be implemented despite cold, rain, fog or rocky terrain.
’For the harvester, forest is a challenging environment,’ Heikkonen concludes.
Read more: Use of AI in the forest sector illustrated in six images
Read more: Drones bring in forest data that used only to be dreamed of